As electric vehicles (EVs) and smart devices continue to proliferate, the demand for lithium-ion batteries is skyrocketing.
Alongside this, the recycling of these batteries—particularly the intermediate product known as Black Mass (BM)
—has become a key focus in the push for sustainable resource utilization.
In this article, we break down the full recycling process of Black Mass:
how it’s created, processed, and transformed into valuable materials once again.
◆ What is Black Mass?
Black Mass is the powder-like intermediate material obtained after spent lithium-ion batteries are discharged, dismantled,
and shredded, followed by a mechanical separation process. It contains high concentrations of valuable metals, including:
- Lithium (Li)
- Cobalt (Co)
- Nickel (Ni)
- Manganese (Mn)
- Carbon (Graphite)
BM is not the final product but a crucial feedstock used to extract and refine these metals for reuse in new batteries and other applications.
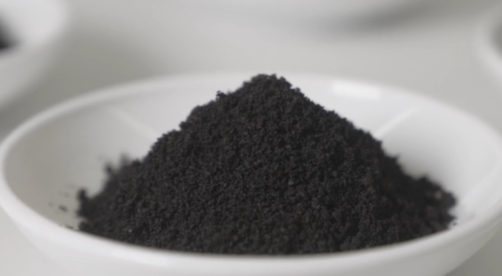
◆ The Black Mass Recycling Process
The recycling of BM typically involves the following stages:
1. Battery Collection & Pre-Treatment
Used lithium-ion batteries are safely discharged and dismantled.
Casing materials are removed, and the cells are shredded into smaller pieces for further separation.
2. Mechanical Separation
The shredded material is sorted to remove aluminum, copper, and plastic fractions.
The remaining fine, dark powder is Black Mass, which contains a concentrated mix of battery metals.
3. Chemical Processing: Hydrometallurgy or Pyrometallurgy
▸ Hydrometallurgical Process
- BM is dissolved in acid (typically sulfuric acid).
- Valuable metal ions are separated using solvent extraction, precipitation, or other chemical methods.
- Metals like Li, Co, Ni are individually recovered from the solution.
▸ Pyrometallurgical Process
- BM is treated in a high-temperature furnace to separate metals from slag.
- The resulting alloy and residue are further refined to isolate specific metals.
🔍 Note: Hydrometallurgy is gaining popularity due to lower energy consumption, higher recovery rates, and reduced environmental impact.
4. Purification & Final Product
Recovered metals are purified and converted into battery-grade materials such as cathode precursors or lithium salts.
Some carbon fractions may also be reused in different industrial applications.
◆ Technical Challenges & Outlook
While promising, Black Mass recycling comes with several technical challenges:
- Variability in metal content depending on battery type and degradation level
- Efficient lithium recovery, which remains technically complex
- High processing costs and energy requirements
- Environmental management, including effluent and emissions treatment
To overcome these, companies are investing in innovative technologies aimed at improving recovery efficiency while minimizing environmental impact.
◆ Dainen Materials’ Global Approach
At Dainen Materials, our Black Mass processing operations are based in India,
allowing us to serve the global market with flexibility and speed.
Our strengths include:
- Stringent quality control throughout the recycling process
- Scalable infrastructure to handle diverse battery feedstock
- A reliable supply chain that meets regional regulations and standards
- Preparation for direct exports to markets such as China in response to upcoming regulatory shifts
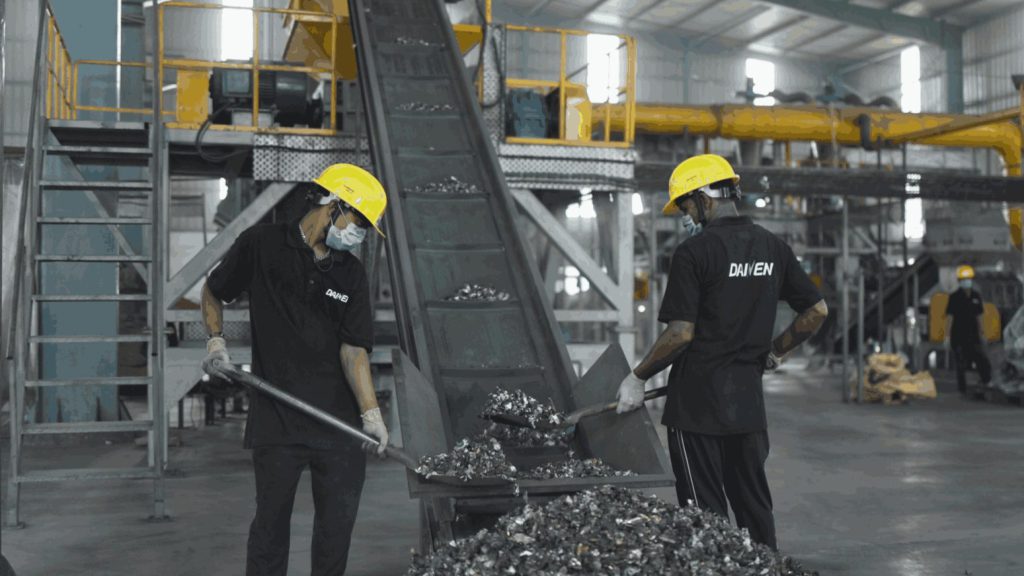
◆ Conclusion
Black Mass recycling is central to closing the loop in the battery supply chain.
As demand for sustainable and traceable materials increases, the role of high-quality,
professionally processed BM becomes even more critical.
Dainen Materials is committed to being a trusted global partner
—driving innovation in resource recovery and contributing to a cleaner, circular future.